Uncoiling Feeding Laser Cutting Machine | Sheet Metal Laser Cutter - Hymson
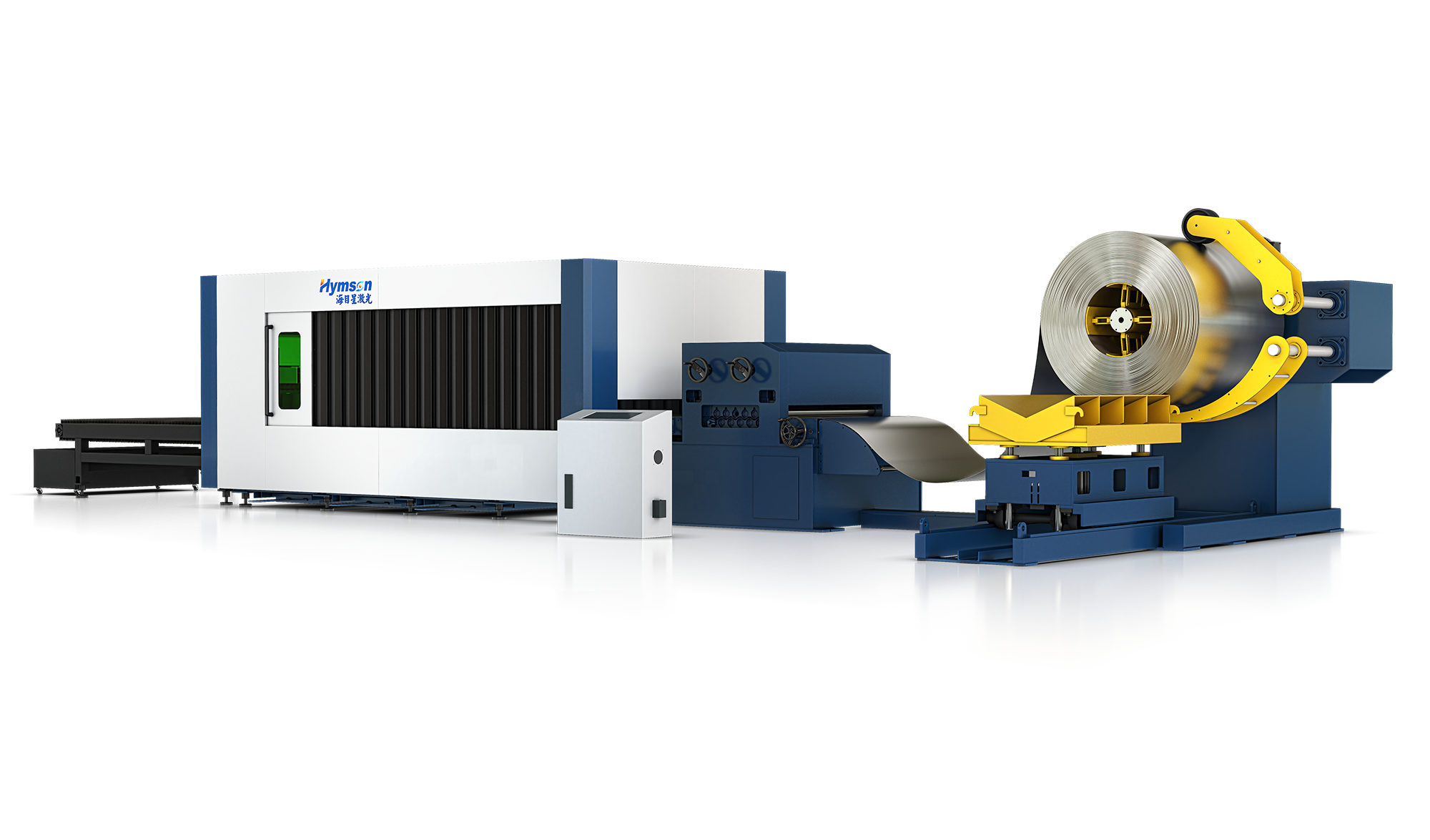
The automatic coil flexible cutting production line is composed of the loading machine, uncoiling machine, precision six-roll skin pass mill, main machine of laser cutting machine, unloading unit and electrical control system to realize the automatic integrated production of coil materials.
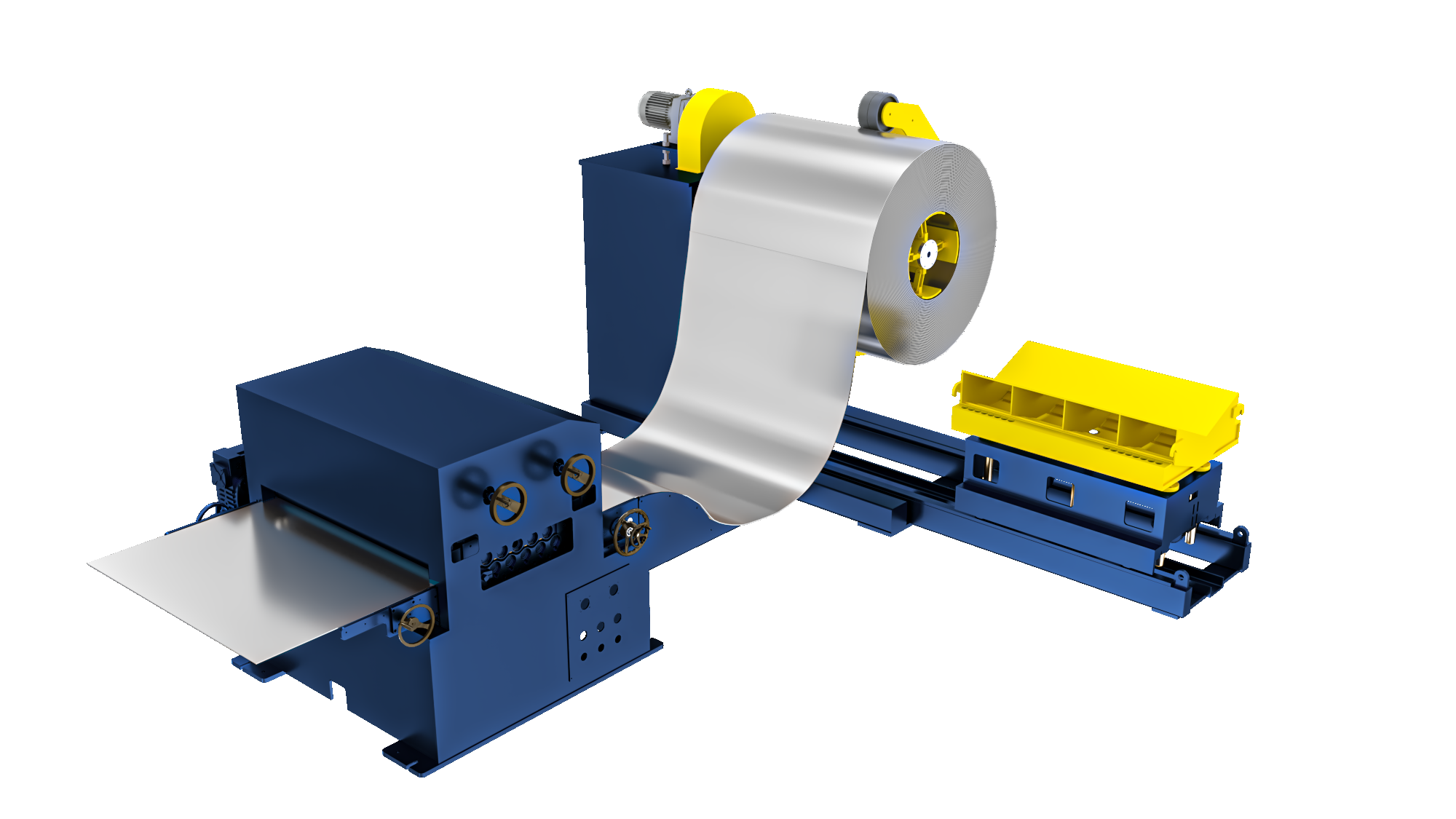
The 15T Structure of Skin Pass Mill Six-Roll-fiber laser cutting machine, equipment for the full CNC operation, easy to use and maintain.
The process: 15T Uncoiling (with pressure arm, hydraulic loading cart, hydraulic corbel ) → snubber →feeding with Six-Roll mill line → laser cutting
The lathe bed processing has undergone high temperature processing to eliminate the material’s internal stress and that produced during welding, to ensure high strength, high precision, and high tolerance.
The middle intelligent partition is used for air extraction and dust removal, and the corresponding air outlet is automatically opened with the cutting range to reduce dust diffusion during the cutting process.

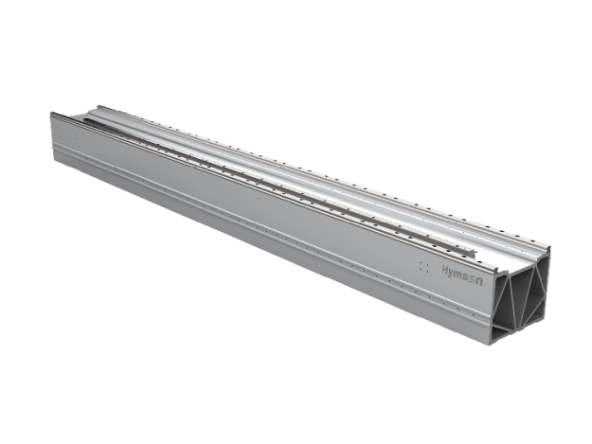
Adopt Hymson’s patent to draw aluminum beam structure, the overall weight is light, high tensile strength, and superior dynamic performance.
Through simulation data analysis and running tests of different type lengths, to ensure the quality, rigidity and dynamics of the beam in long-term operation.
The maximum deformation under the acceleration of 1.5G is only 0.01317mm (finite element analysis of the beam), which is far higher than the industry standard.
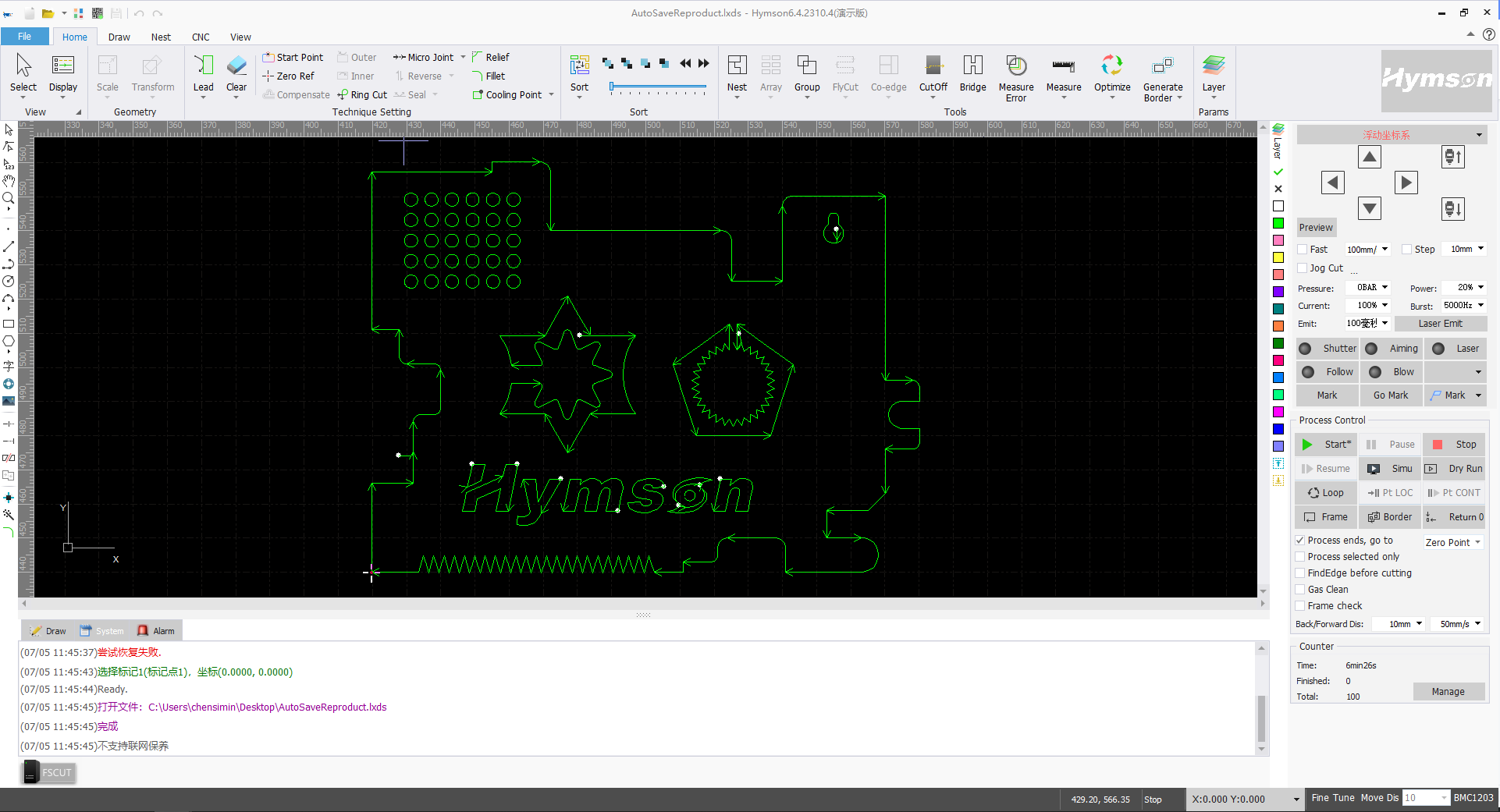
As FSCUT system, it is a highly cost-effective laser cutting CNC system. The system is developed based on EtherCAT bus technology to realize motion control and laser control, cutting gas control, and is widely used in sheet metal, kitchenware and lamps.
It mainly includes laser cutting process processing, common layout functions and laser processing control. The main functions include graphics processing, parameter setting, customized cutting process editing, layout, path planning, simulation, and cutting processing control.
The system can be combined with automatic loading and unloading production lines and flexible production lines of FMS laser cutting to support the automated production.
Aiming at sheet metal applications in different industries, Hymson provides users with professional and high quality product mixes and services, including comprehensive laser automation solutions, such as laser plate cutters, laser tube cutters, laser welding machines, laser automation software, etc.Widely used in engineering machinery, construction machinery, light industrial machinery, agricultural machinery, petroleum machinery, electrical manufacturing, automobile making and aerospace industries.
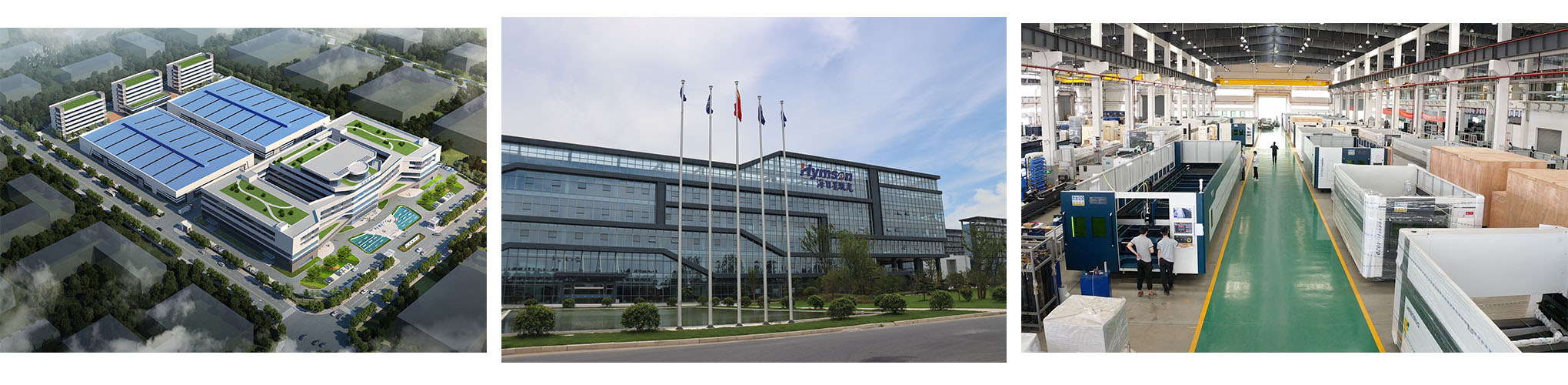
Why choose Hymson laser
● Intelligent dust exhaust system: Work on the cutting area only, strengthen the ventilation effect.● Intelligent gas control system: save gas up to 50%
● Auto-focusing: accurate, fast and smart
● Full-automatic lubrication system: Auto lubricate the gear and rack, maintenance free.
● Installation/training & support by global factory trained engineers.